Nanoglasses
In contrast to traditional metallic glasses, that are prepared by rapid quenching of the melt, nanoglasses are created via a bottom-up approach from amorphous nanoparticles and clusters.
Our expertise lies in multiple methods for preparing nanoglasses and their precursor clusters including inert gas cooling (IGC), laser ablation, sputtering, and cluster ion beam depostion. The properties of the resulting nanoglasses are then compared to traditionally prepared metallic glasses via a vast variety of analysis methods such as XRD, TEM, SEM, EXAFS, SAXS, Mössbauer spectroscopy, ATP and many more.
Group Leader
Mechanical synthesis and mechanical properties of nanomaterials
+49 721 608-26961
julia ivanisenko ∂does-not-exist.kit edu
Karlsruhe Institute of Technology (KIT)
Institute of Nanotechnology
Hermann-von-Helmholtz-Platz 1
76344 Eggenstein-Leopoldshafen, Germany
Understanding Nanoglasses
Metallic nanoglasses represent a novel development in the field of disordered materials, which was initiated by our research group. In contrast to the metallic glasses, which have been widely reported in the literature and are synthesized by rapid quenching from the molten state, nanoglasses are prepared by consolidation (compaction) of nanoparticles, i.e. completely in the solid state.
It has been demonstrated that nanoglasses exhibit a different structure and as a consequence also different properties compared to rapidly-quenched glasses. Clearly, the presence of the internal nanostructure is the prerequisite of the modified properties.
Metallic nanoglasses have been initially synthesized using the well-established Inert Gas Condensation (IGC) technique, using thermal evaporation of an alloy. As the evaporation is performed in an inert gas atmosphere, nanoparticles are formed, typically in the size range of 5 to 20 nm (average) controlled by the synthesis parameters (total pressure of the inert gas, partial pressure of the evaporating alloy components and type of inert gas). The nanoparticles are transported by the convective inert gas flow from the hot source to a liquid nitrogen cooled cylindrical collector. The nanoparticulate powder is collected and then scraped from the surface of the cold finger, and transferred to an in situ (vacuum) compaction device. The nanopowder is compacted at pressures up to 2 GPa, and subsequently, can be compacted further in an ex situ compaction device, typically up to pressures of 6 GPa.
Alternatively, a sputtering source can be used instead of the thermal evaporation source, thus allowing the preparation of alloys consisting of elements with different vapor pressures. A third alternative is the use of laser ablation in order to vaporize the master alloy. In our group all three systems are employed to prepare a variety of metallic nanoglasses of different material systems.
In order to prepare even smaller building blocks for the controlled assembly of nanoglasses, we have developed a cluster ion beam deposition system. In this system, clusters containing typically 50 to 1000 atoms, i.e., smaller than 3 nm in diameter, are prepared using a sputter source, and subsequently formed into a cluster ion beam, which can be manipulated inside a UHV beamline by means of electrical and magnetic fields. Using a 90° bending magnet, size selected clusters can be prepared. The impact energy of the cluster ions can be controlled by means of electric fields, from soft landing to hard landing on the substrates, resulting in a variety of different amorphous structures.
Furthermore, nanoglass structures can be prepared by sputtering thin and thick films of the respective alloys under certain deposition parameters, such as gas pressure, angle of deposition, etc. With the correct parameters, columnar structures can be obtained, which resemble the structures observed using the compaction route described above.
Using the above synthesis routes, our group has synthesized many different amorphous alloy systems in the nanoglass structure, including PdSi, FeSc, CuZr, CuSc using the compaction route starting from nanoparticles, and NiTiCu, PdSi and TiZrCuPd films using the film sputtering technique.
We have employed many different techniques to analyze the structure of nanoglasses and always compared the results with the structure of reference glasses, prepared by rapid quenching from the melt. The characterization techniques include conventional X-ray diffraction (XRD), determination of the radial distribution function (RDF) using synchrotron radiation and transmission electron microscopy , EXAFS, SAXS, Mössbauer spectroscopy (MS), positron annihilation spectroscopy (PAS), scanning (SEM) and transmission (TEM) electron microscopy, atom probe tomography (APT), atomic force (AFM) and scanning tunneling (STM) microscopy, and others.
The current understanding based on the results of the above mentioned techniques of the structure of nanoglasses is as follows:
- In the nanoglass structure two distinct atomic environments are identified, while in rapidly quenched amorphous alloys of identical composition only one atomic environment is observed (concluded from results of TEM, AFM, STM, SAXS, PAS, MS, APT).
- One component corresponds in respect of its structure and atomic environment to that of the rapidly quenched material, while the other component, called interfacial component, is characterized by a different chemical composition and by an increased free volume.
- The interfacial component only appears after compaction of the amorphous nanoparticles.
- The interfacial structure is well defined (as seen from the line width of MS) and seems to exhibit a higher degree of short- and medium range order (as concluded from the RDF), compared to the well defined rapidly quenched structure.
- The free volume of the interfacial component is substantially larger than that of the rapidly quenched material.
As a consequence of the structural differences between the nanoglasses and the rapidly quenched counterparts, also the mechanical, magnetic and thermal properties are drastically different.
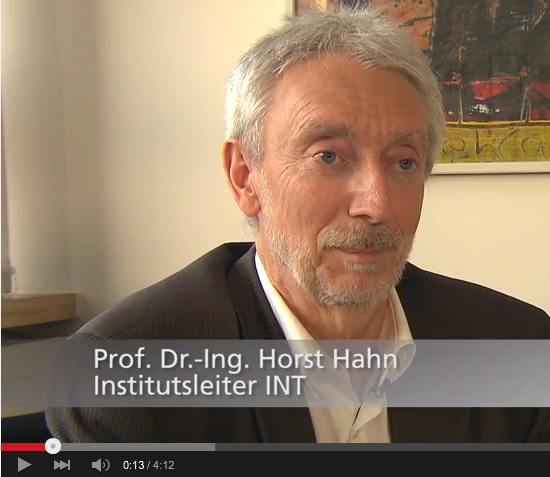
Learn more about Nanoglass in this interview with our institute director, Professor Horst Hahn, on YouTube (German).
Watch the videoSelected Publications
-
Enhanced diffusion in thin-film Cu-Zr nanoglasses
Aaron Rigoni, C.; Boltynjuk, E.; Voigt, H.; Rösner, H.; Tyler, B.; Hahn, H.; Divinski, S. V.; Wilde, G.
2024. Acta Materialia, 265, Art-Nr.: 119634. doi:10.1016/j.actamat.2023.119634 -
In situ TEM studies of relaxation dynamics and crystal nucleation in thin film nanoglasses
Voigt, H.; Rigoni, A.; Boltynjuk, E.; Rösner, H.; Hahn, H.; Wilde, G.
2023. Materials Research Letters, 11 (12), 1022–1030. doi:10.1080/21663831.2023.2278597 -
Enhanced activity and durability of FeCoCrMoCBY nanoglass in acidic hydrogen evolution reaction
Yan, M.; Chen, S.; Wu, S.; Zhou, X.; Fu, S.; Wang, D.; Kübel, C.; Hahn, H.; Lan, S.; Feng, T.
2024. Journal of Materials Science & Technology, 170, 212–220. doi:10.1016/j.jmst.2023.05.067 -
Nanoscale Confinement of Dip‐Pen Nanolithography Written Phospholipid Structures on CuZr Nanoglasses
Vasantham, S. K.; Boltynjuk, E.; Nandam, S. H.; Berganza Eguiarte, E.; Fuchs, H.; Hahn, H.; Hirtz, M.
2024. Advanced Materials Interfaces, 11 (2), Art.-Nr.: 2300721. doi:10.1002/admi.202300721 -
Enhanced specific heat of the Sc79Fe21 nanoglass compared to the Sc79Fe21 amorphous melt-spun ribbon in a temperature range of 150–300 K
Wang, C.; Hu, Q.; Luo, J.; Yin, N.; Shi, Q.; Gleiter, H.; Hahn, H.
2023. Materials Letters, 349, 134706. doi:10.1016/j.matlet.2023.134706 -
Evidence for Glass–glass Interfaces in a Columnar Cu–Zr Nanoglass
Voigt, H.; Rigoni, A.; Boltynjuk, E.; Chellali, M. R.; Tyler, B.; Rösner, H.; Divinski, S.; Hahn, H.; Wilde, G.
2023. Advanced Functional Materials, 33 (44), Art.-Nr.: 2302386. doi:10.1002/adfm.202302386 -
Nano-alloying and nano-chemistry of the immiscible elements Fe and Cu in a FeSc–Cu nanoglass
Singh, S. P.; Chellali, M. R.; Boll, T.; Gleiter, H.; Hahn, H.
2023. Materials Advances, 4 (12), 2604–2611. doi:10.1039/d3ma00167a -
Direct Urea/H
O Fuel Cell with a Hierarchical Porous Nanoglass Anode for High-Efficiency Energy Conversion
Pei, C.; Pei, C.; Chen, S.; Zhou, M.; Chen, X.; Sun, B.; Lan, S.; Hahn, H.
2023. ACS Applied Materials and Interfaces, 15 (20), 24319–24328. doi:10.1021/acsami.3c00774 -
From patterning heterogeneity to nanoglass: A new approach to harden and toughen metallic glasses
Wang, Y.; Gleiter, H.; Li, M.
2022. MRS Bulletin, 48 (1), 56–67. doi:10.1557/s43577-022-00347-w -
Strain rate sensitivity of a Cu
Zr metallic and nanoglass
Sharma, A.; Hirmukhe, S. S.; Nandam, S. H.; Hahn, H.; Singh, I.; Narayan, R. L.; Prasad, K. E.
2022. Journal of Alloys and Compounds, 921, Art.-Nr.: 165991. doi:10.1016/j.jallcom.2022.165991 -
Investigation of softening induced indentation size effect in Nanoglass and Metallic glasss
Hirmukhe, S. S.; Sharma, A.; Nandam, S. H.; Hahn, H.; Prasad, K. E.; Singh, I.
2022. Journal of Non-Crystalline Solids, 577, Art. Nr.: 121316. doi:10.1016/j.jnoncrysol.2021.121316 -
Excess free volume and structural properties of inert gas condensation synthesized nanoparticles based CuZr nanoglasses
Zheng, K.; Yuan, S.; Hahn, H.; Branicio, P. S.
2021. Scientific reports, 11 (1), Art.Nr.: 19246. doi:10.1038/s41598-021-98494-8 -
Evaluation of Microstructure, Mechanical and Thermal Properties of Ti–Zr–Pd–Cu and Ti–Zr–Pd–Cu–Bi Nanoglass Thin Films
Mohri, M.; Chellali, M. R.; Wang, D.; Ivanisenko, J.
2022. Metals and Materials International, 28, 1650–1661. doi:10.1007/s12540-021-01051-1 -
Effect of Structural Relaxation on the Indentation Size Effect and Deformation Behavior of Cu–Zr–Based Nanoglasses
Sharma, A.; Nandam, S. H.; Hahn, H.; Prasad, K. E.
2021. Frontiers in Materials, 8, Art. Nr.: 676764. doi:10.3389/fmats.2021.676764 -
Controlling shear band instability by nanoscale heterogeneities in metallic nanoglasses
Nandam, S. H.; Schwaiger, R.; Kobler, A.; Kübel, C.; Wang, C.; Ivanisenko, Y.; Hahn, H.
2021. Journal of materials research, 36, 2903–2914. doi:10.1557/s43578-021-00285-4 -
On the differences in shear band characteristics between a binary Pd-Si metallic and nanoglass
Sharma, A.; Nandam, S. H.; Hahn, H.; Prasad, K. E.
2021. Scripta materialia, 191, 17–22. doi:10.1016/j.scriptamat.2020.09.009 -
Magnetic Tb
Fe Nanoglass for Cryogenic Permanent Magnet Undulator
Singh, S. P.; Witte, R.; Clemens, O.; Sarkar, A.; Velasco, L.; Kruk, R.; Hahn, H.
2020. ACS applied nano materials, 3 (7), 7281–7290. doi:10.1021/acsanm.0c01674 -
Ni
Nb Nanoglass for Tunable Magnetism and Methanol Oxidation
Baksi, A.; Nandam, S. H.; Wang, D.; Kruk, R.; Chellali, M. R.; Ivanisenko, J.; Gallino, I.; Hahn, H.; Bag, S.
2020. ACS applied nano materials, 3 (7), 7252–7259. doi:10.1021/acsanm.0c01584 -
Nanoglass–Nanocrystal Composite - a Novel Material Class for Enhanced Strength–Plasticity Synergy
Katnagallu, S.; Wu, G.; Singh, S. P.; Nandam, S. H.; Xia, W.; Stephenson, L. T.; Gleiter, H.; Schwaiger, R.; Hahn, H.; Herbig, M.; Raabe, D.; Gault, B.; Balachandran, S.
2020. Small, 16 (39), Art.-Nr. 2004400. doi:10.1002/smll.202004400 -
Nonenzymatic Glucose Sensing Using Ni60Nb40 Nanoglass
Bag, S.; Baksi, A.; Nandam, S. H.; Wang, D.; Ye, X.; Ghosh, J.; Pradeep, T.; Hahn, H.
2020. ACS nano, 14 (5), 5543–5552. doi:10.1021/acsnano.9b09778 -
Influence of topological structure and chemical segregation on the thermal and mechanical properties of Pd–Si nanoglasses
Nandam, S. H.; Adjaoud, O.; Schwaiger, R.; Ivanisenko, Y.; Chellali, M. R.; Wang, D.; Albe, K.; Hahn, H.
2020. Acta materialia, 193, 252–260. doi:10.1016/j.actamat.2020.03.021 -
Elastic Moduli of Nanoglasses and Melt-Spun Metallic Glasses by Ultrasonic Time-of-Flight Measurements
Arnold, W.; Birringer, R.; Braun, C.; Gleiter, H.; Hahn, H.; Nandam, S. H.; Singh, S. P.
2020. Transactions of the Indian Institute of Metals, 73 (5), 1363–1371. doi:10.1007/s12666-020-01969-x -
Deformation-induced atomic rearrangements and crystallization in the shear bands of a Tb75Fe25 nanoglass
Singh, S. P.; Chellali, M. R.; Velasco, L.; Ivanisenko, Y.; Boltynjuk, E.; Gleiter, H.; Hahn, H.
2020. Journal of alloys and compounds, 821, Art.-Nr. 153486. doi:10.1016/j.jallcom.2019.153486 -
Magnetic properties of iron clusters in Sc₇₅Fe₂₅ nanoglass
Ghafari, M.; Mu, X.; Bednarcik, J.; Hutchison, W. D.; Gleiter, H.; Campbell, S. J.
2020. Journal of magnetism and magnetic materials, 494, 165819. doi:10.1016/j.jmmm.2019.165819 -
Magnetic contributions to the low-temperature specific heat of Sc
Fe nanoglass
Wang, C.; Palit, M.; Yin, N.; Shi, Q.; Ivanisenko, Y.; Gleiter, H.; Hahn, H.
2019. Journal of applied physics, 125 (4), Article: 045111. doi:10.1063/1.5082579 -
Direct observation of fast surface dynamics in sub-10-nm nanoglass particles
Chen, N.; Wang, D.; Guan, P. F.; Bai, H. Y.; Wang, W. H.; Zhang, Z. J.; Hahn, H.; Gleiter, H.
2019. Applied physics letters, 114 (4), Article: 043103. doi:10.1063/1.5052016 -
Structure and Properties of Nanoglasses
Ivanisenko, Y.; Kübel, C.; Nandam, S. H.; Wang, C.; Mu, X.; Adjaoud, O.; Albe, K.; Hahn, H.
2018. Advanced engineering materials, 20 (12), Article: 1800404. doi:10.1002/adem.201800404 -
Tuning the Curie temperature of Fe90Sc10 nanoglasses by varying the volume fraction and the composition of the interfaces
Wang, C.; Mu, X.; Chellali, M. R.; Kilmametov, A.; Ivanisenko, Y.; Gleiter, H.; Hahn, H.
2019. Scripta materialia, 159, 109–112. doi:10.1016/j.scriptamat.2018.09.025 -
Nanoscale Structural Evolution and Anomalous Mechanical Response of Nanoglasses by Cryogenic Thermal Cycling
Liu, W.-H.; Sun, B. A.; Gleiter, H.; Lan, S.; Tong, Y.; Wang, X.-L.; Hahn, H.; Yang, Y.; Kai, J.-J.; Liu, C. T.
2018. Nano letters, 18 (7), 4188–4194. doi:10.1021/acs.nanolett.8b01007 -
Electrical resistivity and wave character of free electrons in amorphous and nanoglass Sc75Fe25
Ghafari, M.; Hutchison, W. D.; Campbell, S. J.; Gleiter, H.; Hahn, H.; Feng, T.
2018. Journal of physics / Condensed matter, 30 (2), Art. Nr.: 025702. doi:10.1088/1361-648X/aa9adf -
A novel Ti-based nanoglass composite with submicron–nanometer-sized hierarchical structures to modulate osteoblast behaviors
Chen, N.; Shi, X.; Witte, R.; Nakayama, K. S.; Ohmura, K.; Wu, H.; Takeuchi, A.; Hahn, H.; Esashi, M.; Gleiter, H.; Inoue, A.; Louzguine, D. V.
2013. Journal of materials chemistry / B, 1 (20), 2568–2574. doi:10.1039/c3tb20153h -
Corrigendum to “Atomic structure of Fe 90 Sc 10 glassy nanoparticles and nanoglasses” [Scr. Mater. 139 (2007) 9–12] (Erratum)
Wang, C.; Guo, X.; Ivanisenko, Y.; Goel, S.; Nirschl, H.; Gleiter, H.; Hahn, H.
2018. Scripta materialia, 146, 349. doi:10.1016/j.scriptamat.2017.11.024 -
Effect of elemental segregation on mechanical properties of metallic nanoglasses
Nandam, S. H.; Schwaiger, R.; Wang, D.; Chellali, R.; Ivanisenko, Y.; Hahn, H.
2018. DPG-Frühjahrstagung der Sektion Kondensierte Materie gemeinsam mit der EPS (2018), Berlin, Germany, March 11–16, 2018 -
Ni-Ti nanoglasses: amorphous structure, and magnetic properties
Chellali, M. R.; Nandam, S. H.; Li, S.; Estrada, L. V.; Kruk, R.; Hahn, H.
2018. DPG-Frühjahrstagung der Sektion Kondensierte Materie gemeinsam mit der EPS (2018), Berlin, Germany, March 11–16, 2018 -
Synthesis and characterization of Tb75Fe25 nanoglass
Singh, S. P.; Gleiter, H.; Hahn, H.
2018. DPG-Frühjahrstagung der Sektion Kondensierte Materie gemeinsam mit der EPS (2018), Berlin, Germany, March 11–16, 2018 -
Low temperature structural stability of Fe₉₀Sc₁₀ nanoglasses
Wang, C.; Feng, T.; Wang, D.; Mu, X.; Ghafari, M.; Witte, R.; Kobler, A.; Kübel, C.; Ivanisenko, Y.; Gleiter, H.; Hahn, H.
2018. Materials Research Letters, 6 (3), 178–183. doi:10.1080/21663831.2018.1430622 -
Cu-Zr nanoglasses : Atomic structure, thermal stability and indentation properties
Nandam, S. H.; Ivanisenko, Y.; Schwaiger, R.; Śniadecki, Z.; Mu, X.; Wang, D.; Chellali, R.; Boll, T.; Kilmametov, A.; Bergfeldt, T.; Gleiter, H.; Hahn, H.
2017. Acta materialia, 136, 181–189. doi:10.1016/j.actamat.2017.07.001 -
Atomic structure of Fe90Sc10 glassy nanoparticles and nanoglasses
Wang, C.; Guo, X.; Ivanisenko, Y.; Goel, S.; Nirschl, H.; Gleiter, H.; Hahn, H.
2017. Scripta materialia, 139, 9–12. doi:10.1016/j.scriptamat.2017.06.007 -
Ni-P nanoglass prepared by multi-phase pulsed electrodeposition
Guo, C.; Fang, Y.; Wu, B.; Lan, S.; Peng, G.; Wang, X.-L.; Hahn, H.; Gleiter, H.; Feng, T.
2016. Materials Research Letters, 5 (5), 293–299. doi:10.1080/21663831.2016.1264495 -
Surface segregation of primary glassy nanoparticles of Fe90Sc10 nanoglass
Wang, C.; Wang, D.; Mu, X.; Goel, S.; Feng, T.; Ivanisenko, Y.; Hahn, H.; Gleiter, H.
2016. Materials letters, 181, 248–252. doi:10.1016/j.matlet.2016.05.189 -
Nanoglasses: A New Kind of Noncrystalline Material and the Way to an Age of New Technologies?
Gleiter, H.
2016. Small, 12 (16), 2225–2233. doi:10.1002/smll.201500899 -
Sample size effects on strength and deformation mechanism of Sc₇₅Fe₂₅ nanoglass and metallic glass
Wang, X.; Jiang, F.; Hahn, H.; Li, J.; Gleiter, H.; Sun, J.; Fang, J.
2016. Scripta Materialia, 116, 95–99. doi:10.1016/j.scriptamat.2016.01.036 -
Mechanisms of Nanoglass Ultrastability
Danilov, D.; Hahn, H.; Gleiter, H.; Wenzel, W.
2016. ACS Nano, 10 (3), 3241–3247. doi:10.1021/acsnano.5b05897 -
Nanoscale morphology of Ni₅₀Ti₄₅Cu₅ nanoglass
Sniadecki, Z.; Wang, D.; Ivanisenko, Y.; Chakravadhanula, V. S. K.; Kübel, C.; Hahn, H.; Gleiter, H.
2016. Materials characterization, 113, 26–33. doi:10.1016/j.matchar.2015.12.025 -
A nanoglass alloying immiscible Fe and Cu at the nanoscale
Chen, N.; Wang, D.; Feng, T.; Kruk, R.; Yao, K. F.; Louzguine-Luzgin, D. V.; Hahn, H.; Gleiter, H.
2015. Nanoscale, 7, 6607–6611. doi:10.1039/C5NR01406A -
Plasticity of a scandium-based nanoglass
Wang, X. L.; Jiang, F.; Hahn, H.; Gleiter, H.; Sun, J.; Fang, J. X.
2015. Scripta materialia, 98, 40–43. doi:10.1016/j.scriptamat.2014.11.010 -
Influence of interface on structure and magnetic properties of Fe₅₀B₅₀ nanoglass
Stoesser, A.; Ghafari, M.; Klimametov, A.; Gleiter, H.; Sakurai, Y.; Itou, M.; Kohara, S.; Hahn, H.; Kamali, S.
2014. Journal of applied physics, 116, 134305/1–7. doi:10.1063/1.4897153 -
Thermal and plastic behavior of nanoglasses
Franke, O.; Leisen, D.; Gleiter, H.; Hahn, H.
2014. Journal of materials research, 29, 1210–1216. doi:10.1557/jmr.2014.101 -
Nanoglasses: A new kind of noncrystalline materials
Gleiter, H.
2013. Beilstein Journal of Nanotechnology, 4, 517–533. doi:10.3762/bjnano.4.61 -
Evidence for enhanced ferromagnetism in an iron-based nanoglass
Witte, R.; Feng, T.; Fang, J. X.; Fischer, A.; Ghafari, M.; Kruk, R.; Brand, R. A.; Wang, D.; Hahn, H.; Gleiter, H.
2013. Applied physics letters, 103, 073106/1–5. doi:10.1063/1.4818493 -
Structural investigations of interfaces in Fe₉₀Sc₁₀ nanoglasses using high-energy x-ray diffraction
Ghafari, M.; Kohara, S.; Hahn, H.; Gleiter, H.; Feng, T.; Witte, R.; Kamali, S.
2012. Applied Physics Letters, 100, 133111/1–4. doi:10.1063/1.3699228 -
Evidence of itinerant magnetism in a metallic nanoglass
Ghafari, M.; Hahn, H.; Gleiter, H.; Sakurai, Y.; Itou, M.; Kamali, S.
2012. Applied Physics Letters, 101, 243104/1–4. doi:10.1063/1.4769816 -
Atomic structure and structural stability of Sc₇₅Fe₂₅ nanoglasses
Fang, J. X.; Vainio, U.; Puff, W.; Würschum, R.; Wang, X. L.; Wang, D.; Ghafari, M.; Jiang, F.; Sun, J.; Hahn, H.; Gleiter, H.
2012. Nano Letters, 12, 458–463. doi:10.1021/nl2038216 -
Short range order around Sc atoms in Fe₉₀Sc₁₀ nanoglasses using fluorescence X-ray absorption spectroscopy
Leon, A.; Rothe, J.; Hahn, H.; Gleiter, H.
2012. Revue de Metallurgie, 109, 35–39. doi:10.1051/metal/2011079 -
Structure, stability and mechanical proeprties of internal interfaces in Cu₆₄Zr₃₆ nanoglasses studied by MD simulations
Ritter, Y.; Sopu, D.; Gleiter, H.; Albe, K.
2011. Acta Materialia, 59, 6588–6593. doi:10.1016/j.actamat.2011.07.013