Mechanical Synthesis and Properties of Nanomaterials
Materials with very small grain sizes – nano- and submicrocrystalline – demonstrate attractive mechanical properties and unusual deformation behavior. Our aim is to propose physical mechanisms explaining these features, to explore new materials with enhanced mechanical properties, and to develop advanced synthesis and processing techniques, using severe plastic deformation and high-end analysis methods.
Group Leader
Mechanical synthesis and mechanical properties of nanomaterials
+49 721 608-26961
julia ivanisenko ∂does-not-exist.kit edu
Karlsruhe Institute of Technology (KIT)
Institute of Nanotechnology
Hermann-von-Helmholtz-Platz 1
76344 Eggenstein-Leopoldshafen, Germany
Our Motivation
At INT nanostructured materials are produced using various methods: "bottom-up" syntheses like inert gas condensation (IGC) and layer deposition, and a "top-down" approach based on severe plastic deformation (SPD) for microstructure refinement. In particular, high pressure torsion (HPT) is established at INT as SPD technique for the synthesis of nanostructured metals and alloys possessing sub-micron or even nanometer-sized grains. HPT is a powerful tool for microstructure design at different hierarchical levels. This includes, in addition to grain size refinement, grain boundary design, texture formation, mechanically driven phase transformation, and the formation of metastable phases. Recently we developped a new technique called High Pressure Torsion Extrusion (HPTE), a scaled-up HPT method for processing of advanced nanocrystalline materials in amounts reasonable for industrial applications. In addition to a conventional mechanical testing machine (ZwickRoell, Ulm, Germany) we use a custom-built tensile stage specially designed for miniature specimens and equipped with a laser extensometer for precise strain measurements. Characterizations of the samples' microstructures are performed using XRD analysis, EBSD-SEM and a variety of TEM methods in collaboration with the Electron Microscopy and Spectroscopy Group (EMSG) of Prof. Dr. Christian Kübel.
(a) Schematic diagram of HPT; (b) engineering stress–strain curve of HPT-processed Pd20Ag80 alloy. Grain refinement down to 120 nm, as shown in dark field TEM image (inset); find out more
Current Research Projects
1. High Pressure Torsion Extrusion: A Scale-Up of HPT
2. Mechanical Behaviour of Nanoglasses
3. Mechanically Driven Phase Transformations
4. Mechanical Behavior of Nanocrystalline High Entropy Alloys
5. High-strength Al-based Alloys with High Electric Conductivity
6. Fatigue and Corrosion Performance of Ultrafine-Grained Mg-Based Alloys
1. High Pressure Torsion Extrusion: A Scale-Up of HPT
In collaboration with Brigitte Baretzky (INT) we scaled up the HPT method for the processing of advanced nanocrystalline materials in amounts reasonable for industrial applications. The new method is named High Pressure Torsion Extrusion (HPTE). During HPTE, a rod-shape specimen is extruded through sectional containers rotating relative to each other (Fig. 2). The specimen is subjected to shear deformation in the area where the containers meet. One of the main advantages of the HPTE process is that already after a single extrusion pass a high accumulated strain (orders of magnitude lager than for Equal Channel Angular Pressing, Twist Extrusion, Cyclic Extrusion Compression, etc.) can be achieved in the specimen. At present, commercially pure copper and electro-technical Al alloy 6101 were successfully processed using HPTE. As a result uniform UFG microstructure was formed and high mechanical properties were achieved.
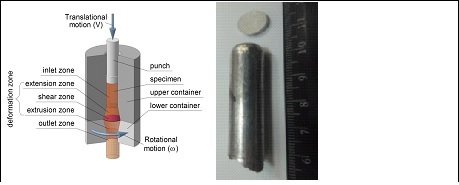
Furthermore, the presence of a strong velocity gradient in the specimen cross-section during HPTE provides the possibility to process hybrid materials or composite parts with helical architecture of functional elements. Simulations predict that such composites can combine high strength and ductility. This approach is being studied now in the frames of a German Research Society (Deutsche Forschungsgemeinschaft, DFG) Project „Hybrid ultrafine grained materials produced by high pressure torsion extrusion” (IV98/8-1, 2017-2020).
Publications
- Device and method for forming components made of metallic materials V. Fedorov, Yu. Ivanisenko, B. Baretzky, and H. Hahn, European patent EP 2 821 156 B1
- High Pressure Torsion Extrusion as a new severe plastic deformation process Yu. Ivanisenko, R. Kulagin, V. Fedorov, A. Mazilkin, T. Scherer, B. Baretzky, and H. Hahn Mat. Sci. Eng. 2016, A664: 247-256, DOI: 10.1016/j.msea.2016.04.008
2. Mechanical behaviour of nanoglasses
In collaboration with R. Schwaiger Group we analyzed the mechanical performance of Cu50Zr50 metallic nanoglasses. We found that the hardness and Young's modulus increase for the nanoglasses compared to melt-spun ribbons. The curves of both as prepared and annealed nanoglass samples are smooth without any pop-ins (indicating homogeneous deformation), while the load vs displacement curves of the melt-spun ribbon of similar composition show clear pop-ins (serrations), indicating the generation of shear bands (inhomogeneous deformation) (Fig. 3a). The area in the vicinity of the Vickers indents in nanoglass (Fig. 3b) clearly does not show any shear bands around the indent whereas the melt-spun ribbons shows shear bands around the indent. It is proposed that the interfacial regions, which are sources of high free volume act as nucleating sites for the formation of numerous shear transformation zones giving rise to homogeneous deformation in nanoglasses.
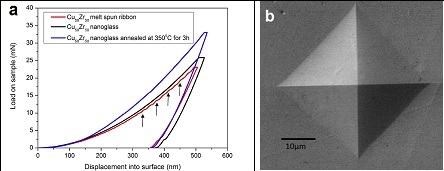
Publications
- Cu-Zr nanoglasses: atomic structure, thermal stability and indentation properties S.H. Nandam, Yu. Ivanisenko, R. Schwaiger, Z. Śniadecki, X. Mu, D. Wang, R. Chellali, T. Boll, A. Kilmametov, T. Bergfeldt, H. Gleiter, and H. Hahn, Acta Materialia 2017, 136, 181-189. DOI: 10.1016/j.actamat.2017.07.001
3. Mechanically driven phase transformations
Being applied to alloys, severe plastic deformation often leads to mechanically driven phase transformations like forced mixing in immiscible alloy systems, decomposition of supersaturated solid solutions, dissolution of second phase particles or even amorphization. In our group we study mechanically driven cementite dissolution in pearlitic steels, mixing in immiscible Cu-Ag or Cu-Nb systems and the formation of high pressure w phase in Ti and Ti alloys. Our aim is to understand the physical mechanisms of these processes.
Publications
- Forced chemical mixing of immiscible Ag-Cu heterointerfaces using high-pressure torsion M. Pouryazdan, D. Schwen, D. Wang, T. Scherer, H. Hahn, R. S. Averback, and P. Bellon, Phys. Rev. B 2012, 86, 144302. DOI: 10.1103/PhysRevB.86.144302
- Transformations of Cu in supersaturated solid solutions under high-pressure torsion B.B. Straumal, A.R. Kilmametov, A.A. Mazilkin, L. Kurmanaeva, Y. Ivanisenko, A. Korneva, P. Zięba, and B. Baretzky, Matt Lett. 2015, 138, 255–258, DOI: 10.1016/j.matlet.2014.10.009
- Phase Transformations in Ti–Fe Alloys Induced by High-Pressure Torsion B.B. Straumal, A.R. Kilmametov, Yu. Ivanisenko, A.S. Gornakova, A.A. Mazilkin, M.J. Kriegel, O.B. Fabrichnaya, B. Baretzky and H. Hahn, Adv. Eng. Mat. 2015, 17, 1835–1841, DOI: 10.1002/adem.201500143
- Self-organized, size-selection of precipitates during severe plastic deformation of dilute Cu-Nb alloys at low temperatures J.A. Beach, M. Wang, P. Bellon, S. Dillon, Yu. Ivanisenko, T. Boll, and R.S. Averback, Acta Mater. 2017, 140, 217-223 DOI:10.1016/j.actamat.2017.08.041
- The α→ω and β→ω phase transformations in Ti–Fe alloys under high-pressure torsion A.R. Kilmametov, Yu. Ivanisenko, A.A. Mazilkin, B.B. Straumal, A.S. Gornakova, O.B. Fabrichnaya, M.J. Kriegel, D. Rafaja, and H. Hahn, Acta Mater. 2017, 144, 337-351, DOI: 10.1016/j.actamat.2017.10.051
4. Mechanical behavior of nanocrystalline high entropy alloys
This project is aimed to establish the influence of the severe plastic deformation by high pressure torsion on the microstructure, phase composition and the resulting mechanical properties of a high entropy alloys.
Publications
- FCC nanostructured TiFeCoNi alloy with multi-scale grains and enhanced plasticity Z. Fu, B. E. MacDonald, D. Zhang; B. Wu, W. Chen, J. Ivanisenko, H. Hahn, E. J. Lavernia, Scripta materialia 2018, 143, 108–112. DOI: 10.1016/j.scriptamat.2017.09.023
- Evolution of Microstructure and Mechanical Properties of a CoCrFeMnNi High-Entropy Alloy during High-Pressure Torsion at Room and Cryogenic Temperatures S. Zherebtsov, N. Stepanov, Yu. Ivanisenko, D. Shaysultanov, N. Yurchenko, M. Klimova, G. Salishchev, Metals 2018, 8(2), 123, DOI: 10.3390/met8020123
5. High-strength Al-based alloys with high electric conductivity
Due to the combination of low weight, good electrical conductivity and technological plasticity, as well as high resistance to atmospheric corrosion, aluminum and a number of alloys based on it are widely used in electrical engineering, displacing more expensive copper-based conductor materials. One of the main disadvantages of aluminum conductors is their low strength compared to copper. The proposed project is focused on the development of a new generation of electric conducting materials with properties enhanced thanks to the microstructure design – a purposeful formation of nanostructures with specified parameters. Alloys under investigation will be nanostructured using an invented at INT KIT method of severe plastic deformation by High Pressure Torsion Extrusion, and subsequently artificially aged to additionally benefit from precipitation hardening. The precipitation kinetics, as well as the subtle structure of precipitates and their distribution in the microstructure is studied in collaboration with Prof. Dr. Christan Kübel using high-end electron microscopy. As a result we plan to produce nanostructured wires of the high strength Al alloys with enhanced electric conductivity.
6. Fatigue and corrosion performance of ultrafine-grained Mg-based alloys
This is a new research project, funded by DFG, which we perform in collaboration with Prof. Dr. Eberhard Kerscher from TU Kaiserslautern. The main aim of the project is to study the microstructure and texture evolution in two model biocompatible Mg alloys during different HPTE routes and subsequent thermal treatment, and the effect of the developed microstructure and texture on the monotonic and cyclic mechanical properties, even in corrosive environments. Application of Mg alloys as implant materials is limited due to their low strength, which is often lower than the human bone strength. Furthermore, they demonstrate low corrosion resistance in the presence of strengthening precipitates. In order to improve the performance of chosen alloys, High Pressure Torsion Extrusion will be used which will allow to increase the strength due to (sub)grain boundary strengthening without forming precipitates which might be critical in corrosive environments.
Publications
Xu, R.; Lu, Y.; Dai, Y.; Debastiani, R.; Hahn, H.; Ivanisenko, Y.
2025. Materials Characterization, 224, Art.-Nr. 114956. doi:10.1016/j.matchar.2025.114956
Lu, Y.; Zhu, G.; Hahn, H.; Ivanisenko, Y.
2024. Materials Research Letters, 12 (7), 525–534. doi:10.1080/21663831.2024.2356761
Xu, R.; Lu, Y.; Dai, Y.; Brognara, A.; Hahn, H.; Ivanisenko, Y.
2024. Journal of Materials Science, 59, 9075–9090. doi:10.1007/s10853-024-09713-2
Lu, Y.; Zhu, G.; Ivanisenko, Y.; Hahn, H.
2024, March 1. doi:10.35097/1937
Nugmanov, D.; Kulagin, R.; Perroud, O.; Mail, M.; Hahn, H.; Ivanisenko, Y.
2023. Journal of Materials Processing Technology, 315, Art.-Nr.: 117932. doi:10.1016/j.jmatprotec.2023.117932
Lu, Y.; Hahn, H.; Ivanisenko, Y.
2022. Advanced Engineering Materials, 25 (9), Art.-Nr. 2201473. doi:10.1002/adem.202201473
Mantha, L. S.; MacDonald, B. E.; Mu, X.; Mazilkin, A.; Ivanisenko, J.; Hahn, H.; Lavernia, E. J.; Katnagallu, S.; Kübel, C.
2021. Acta materialia, 220, Art.Nr.: 117281. doi:10.1016/j.actamat.2021.117281
Nandam, S. H.; Schwaiger, R.; Kobler, A.; Kübel, C.; Wang, C.; Ivanisenko, Y.; Hahn, H.
2021. Journal of materials research, 36, 2903–2914. doi:10.1557/s43578-021-00285-4
Lu, Y.; Mazilkin, A.; Boll, T.; Stepanov, N.; Zherebtzov, S.; Salishchev, G.; Ódor, É.; Ungar, T.; Lavernia, E.; Hahn, H.; Ivanisenko, Y.
2021. Materialia, 16, Art.-Nr.: 101059. doi:10.1016/j.mtla.2021.101059
Mu, X.; Chellali, M. R.; Boltynjuk, E.; Gunderov, D.; Valiev, R. Z.; Hahn, H.; Kübel, C.; Ivanisenko, Y.; Velasco, L.
2021. Advanced Materials, 33 (12), Art.-Nr.: 2007267. doi:10.1002/adma.202007267
Baksi, A.; Nandam, S. H.; Wang, D.; Kruk, R.; Chellali, M. R.; Ivanisenko, J.; Gallino, I.; Hahn, H.; Bag, S.
2020. ACS applied nano materials, 3 (7), 7252–7259. doi:10.1021/acsanm.0c01584
Nandam, S. H.; Adjaoud, O.; Schwaiger, R.; Ivanisenko, Y.; Chellali, M. R.; Wang, D.; Albe, K.; Hahn, H.
2020. Acta materialia, 193, 252–260. doi:10.1016/j.actamat.2020.03.021
Kriegel, M. J.; Rudolph, M.; Kilmametov, A.; Straumal, B. B.; Ivanisenko, J.; Fabrichnaya, O.; Hahn, H.; Rafaja, D.
2020. Metals, 10 (3), Article No. 402. doi:10.3390/met10030402
Singh, S. P.; Chellali, M. R.; Velasco, L.; Ivanisenko, Y.; Boltynjuk, E.; Gleiter, H.; Hahn, H.
2020. Journal of alloys and compounds, 821, Art.-Nr. 153486. doi:10.1016/j.jallcom.2019.153486
Nugmanov, D.; Mazilkin, A.; Hahn, H.; Ivanisenko, Y.
2019. Metals, 9 (10), Art.Nr.: 1081. doi:10.3390/met9101081
Kulagin, R.; Beygelzimer, Y.; Estrin, Y.; Ivanisenko, Y.; Baretzky, B.; Hahn, H.
2019. Metals, 9 (3), 306. doi:10.3390/met9030306
Wang, C.; Palit, M.; Yin, N.; Shi, Q.; Ivanisenko, Y.; Gleiter, H.; Hahn, H.
2019. Journal of applied physics, 125 (4), Article: 045111. doi:10.1063/1.5082579
Kriegel, M. J.; Kilmametov, A.; Rudolph, M.; Straumal, B. B.; Gornakova, A. S.; Stöcker, H.; Ivanisenko, Y.; Fabrichnaya, O.; Hahn, H.; Rafaja, D.
2018. Advanced engineering materials, 20 (4), Art.-Nr.: 1700933. doi:10.1002/adem.201700933
Kriegel, M. J.; Kilmametov, A.; Klemm, V.; Schimpf, C.; Straumal, B. B.; Gornakova, A. S.; Ivanisenko, Y.; Fabrichnaya, O.; Hahn, H.; Rafaja, D.
2019. Advanced engineering materials, 21 (1), 1800158. doi:10.1002/adem.201800158
Ivanisenko, Y.; Kübel, C.; Nandam, S. H.; Wang, C.; Mu, X.; Adjaoud, O.; Albe, K.; Hahn, H.
2018. Advanced engineering materials, 20 (12), Article: 1800404. doi:10.1002/adem.201800404
Fu, Z.; MacDonald, B. E.; Zhang, D.; Wu, B.; Chen, W.; Ivanisenko, J.; Hahn, H.; Lavernia, E. J.
2018. Scripta materialia, 143, 108–112. doi:10.1016/j.scriptamat.2017.09.023
Kulagin, R.; Beygelzimer, Y.; Ivanisenko, Y.; Mazilkin, A.; Straumal, B.; Hahn, H.
2018. Materials letters, 222, 172–175. doi:10.1016/j.matlet.2018.03.200
Kilmametov, A. R.; Ivanisenko, Y.; Straumal, B. B.; Gornakova, A. S.; Mazilkin, A. A.; Hahn, H.
2018. Metals, 8 (1), Art.Nr. 1. doi:10.3390/met8010001
Straumal, B. B.; Kilmametov, A. R.; Ivanisenko, Y.; Mazilkin, A. A.; Valiev, R. Z.; Afonikova, N. S.; Gornakova, A. S.; Hahn, H.
2018. Journal of alloys and compounds, 735, 2281–2286. doi:10.1016/j.jallcom.2017.11.317
Mohri, M.; Wang, D.; Ivanisenko, J.; Gleiter, H.; Hahn, H.
2018. Journal of alloys and compounds, 735, 2197–2204. doi:10.1016/j.jallcom.2017.11.387
Kulagin, R.; Beygelzimer, Y.; Ivanisenko, Y.; Mazilkin, A.; Hahn, H.
2017. Procedia engineering, 207, 1445–1450. doi:10.1016/j.proeng.2017.10.911
Kilmametov, A. R.; Ivanisenko, Y.; Mazilkin, A. A.; Straumal, B. B.; Gornakova, A. S.; Fabrichnaya, O. B.; Kriegel, M. J.; Rafaja, D.; Hahn, H.
2018. Acta materialia, 144, 337–351. doi:10.1016/j.actamat.2017.10.051
MacDonald, B. E.; Fu, Z.; Zheng, B.; Chen, W.; Lin, Y.; Chen, F.; Zhang, L.; Ivanisenko, J.; Zhou, Y.; Hahn, H.; Lavernia, E. J.
2017. JOM, 1–8. doi:10.1007/s11837-017-2484-6
Mohri, M.; Wang, D.; Ivanisenko, J.; Gleiter, H.; Hahn, H.
2017. Materials characterization, 131, 140–147. doi:10.1016/j.matchar.2017.07.014
Nandam, S. H.; Ivanisenko, Y.; Schwaiger, R.; Śniadecki, Z.; Mu, X.; Wang, D.; Chellali, R.; Boll, T.; Kilmametov, A.; Bergfeldt, T.; Gleiter, H.; Hahn, H.
2017. Acta materialia, 136, 181–189. doi:10.1016/j.actamat.2017.07.001
Wang, C.; Guo, X.; Ivanisenko, Y.; Goel, S.; Nirschl, H.; Gleiter, H.; Hahn, H.
2017. Scripta materialia, 139, 9–12. doi:10.1016/j.scriptamat.2017.06.007
Kulagin, R.; Beygelzimer, Y.; Ivanisenko, Y.; Mazilkin, A.; Hahn, H.
2017. 7th International Conference on Nanomaterials by Severe Plastic Deformation (NanoSPD7), Sydney, Australia, 2–7 July 2017. Ed.: Y. Estrin, Art. Nr. 012045, Institute of Physics Publishing Ltd (IOP Publishing Ltd). doi:10.1088/1757-899X/194/1/012045
Kilmametov, A.; Ivanisenko, Y.; Straumal, B.; Mazilkin, A. A.; Gornakova, A. S.; Kriegel, M. J.; Fabrichnaya, O. B.; Rafaja, D.; Hahn, H.
2017. Scripta materialia, 136, 46–49. doi:10.1016/j.scriptamat.2017.04.010
Ivanisenko, Y.; Enikeev, N. A.; Yang, K.; Smoliakov, A.; Soloviev, V. P.; Fecht, H.; Hahn, H.
2016. Materials Science and Engineering A, 668, 255–262. doi:10.1016/j.msea.2016.05.036
Ivanisenko, Y. V.; Kulagin, R.; Fedorov, V. T.; Mazilkin, A. A.; Scherer, T.; Baretzky, B. M. M.; Hahn, H.
2016. Materials science and engineering / A, 664, 247–256. doi:10.1016/j.msea.2016.04.008
Sniadecki, Z.; Wang, D.; Ivanisenko, Y.; Chakravadhanula, V. S. K.; Kübel, C.; Hahn, H.; Gleiter, H.
2016. Materials characterization, 113, 26–33. doi:10.1016/j.matchar.2015.12.025
Straumal, B. B.; Kilmametov, A. R.; Ivanisenko, Y.; Gornakova, A. S.; Mazilkin, A. A.; Kriegel, M. J.; Fabrichnaya, O. B.; Baretzky, B.; Hahn, H.
2015. Advanced engineering materials, 17, 1835–1841. doi:10.1002/adem.201500143
Mohri, M.; Nili-Ahmadabadi, M.; Ivanisenko, J.; Schwaiger, R.; Hahn, H.; Chakravadhanula, V. S. K.
2015. Thin solid films, 583, 245–254. doi:10.1016/j.tsf.2015.03.057
Ivanisenko, Y.; Tabachnikova, E. D.; Psaruk, I. A.; Smirnov, S. N.; Kilmametov, A.; Kobler, A.; Kübel, C.; Kurmanaeva, L.; Csach, K.; Mishkuf, Y.; Scherer, T.; Semerenko, Y. A.; Hahn, H.
2014. International journal of plasticity, 60, 40–57. doi:10.1016/j.ijplas.2014.04.011
Ivanisenko, Y.; Federov, V. T.; Baretzky, B.; Hahn, H.
2014. 6th International Conference on Nanomaterials by Severe Plastic Deformation (NANOSPD 2014), Metz, F, June 30 - July 4, 2014
Fedorov, V. T.; Hahn, H.; Ivanisenko, Y.
2012. Advanced Engineering Materials, 14, 296–298. doi:10.1002/adem.201100306
Ivanisenko, Y.; Darbandi, A.; Dasgupta, S.; Kruk, R.; Hahn, H.
2010. Advanced Engineering Materials, 12, 666–676. doi:10.1002/adem.201000131